The interior of the case is what is protecting your product from damage. The case exterior is built to protect this interior. The proper process to determine the design of the right interior can be a complex one. Here, we will walk through the process.
While there may be instances where a simple foam lining would be appropriate, more often than not, filling a case with foam will not give your equipment the protection that it needs to arrive at its destination unharmed. In fact, more foam will sometimes result in more impact being transmitted to your product.
The process of designing a functional interior begins by examining the product and the anticipated shipping environment.
The first consideration is the fragility of the product. This is expressed in how many “g’s” the product can withstand and is called the product’s “g-factor”. The lower the g-factor, the more fragile the equipment. Determining the correct g-factor is a process that would have a product tested at increasingly severe impacts until damage occurred. Most of our clients don’t allow us to test their equipment to destruction so we need to make educated guesses based on common knowledge and our own experience.
FOR EXAMPLE, THE FOLLOWING ARE APPROXIMATE G-FACTORS FOR A VARIETY OF PRODUCTS:
- 15-25 g’s / Aircraft altimeters, gyroscopes, instruments with delicate mechanical alignments
- 25-40 g’s / Medical diagnostic equipment
- 40-60 g’s / Hard drives, test instruments, display terminals
- 60-85 g’s / Stereos, televisions
- 85-115 g’s / Major appliances, furniture
- 115 g’s plus / Machine tools, stationary equipment, sewing machines
The above chart is very general and should be used as a guide only. Individual product testing may be the only way to determine an accurate g-factor.
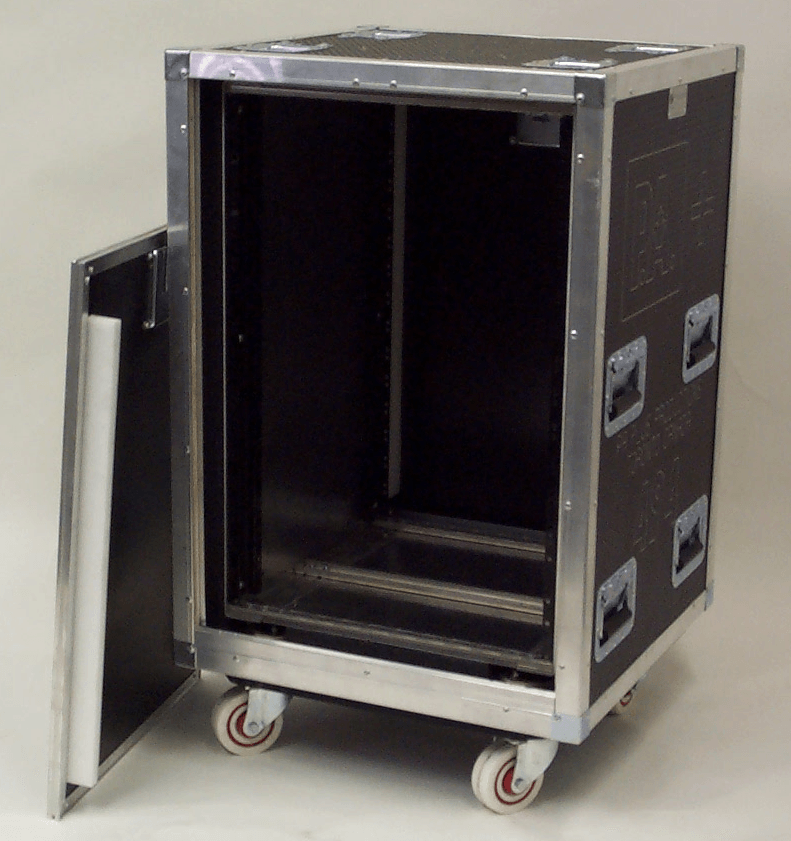
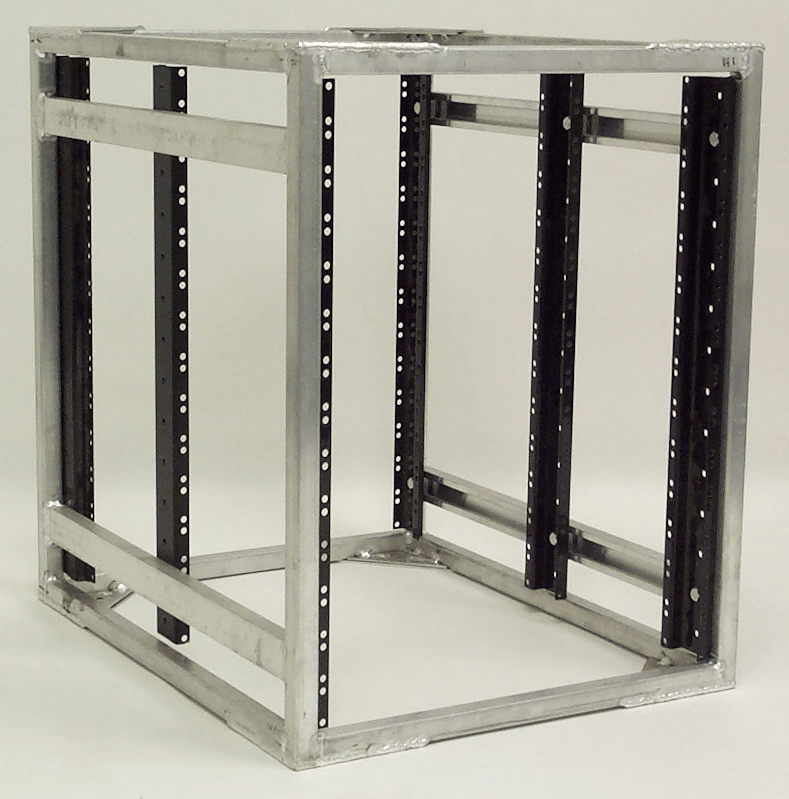
EXAMPLES OF APPROXIMATE DROP-HEIGHTS:
The next factor is to determine the shipping environment, specifically, the drop heights that the product will be subjected to. This can be determined largely, by the weight of the product. For example: If your product weighs 20-50 pounds, it is likely that one person will be carrying each piece. It’s not very likely that that person would drop the product from a height greater than 24″-30″. The following chart will prove useful for determining drop heights.
- 0-10 pounds / One person throwing product / Drop height of 42 inches
- 10-20 pounds / One person carrying (light) / Drop height of 36 inches
- 20-50 pounds / One person carrying (heavy) / Drop height of 30 inches
- 50-100 pounds / Two people carrying / Drop height of 24 inches
- 100-250 pounds / Light equipment handling / Drop height of 18 inches
- 250+ pounds / Heavy equipment handling / Drop height of 12 inches
WITH FRAGILITY AND ANTICIPATED ABUSE DETERMINED, NEXT IS “STATIC LOADING”…
We use Dynamic Cushioning Curves to determine “static loading” which will allow us to determine case size, foam type, foam thickness and cushion size.
In order to absorb impact, your product needs to compress the foam that it is riding on. Not enough to bottom out the product (as can happen with lighter density foams) but enough to extend the moment of impact. Think about how the seatbelt in your car is designed to work. In that scenario, you are the product. You don’t want to bottom out. This is why bungee cords aren’t used as seatbelts.
You can’t simply line a case with foam. If you line a case with 1″ of 2 lb. etha foam and put in a moderately fragile product (g-factor of 50) that weighs 50 pounds and is 12″ square, and you drop this case from 30″, you will subject the equipment to almost 80 g’s. The problem gets much worse in multiple impact situations or where lighter density foam is used.
If you took the same product and put it in a case with the product supported on 4 strategically placed pads of the same foam, each measuring 3.5″ square and 2″ thick, and dropped it from the same height, the equipment will be subjected to less than 40 g’s.
FINAL FEW CONSIDERATIONS
Before we can finish the interior of your case there are a few other factors we need to take into consideration, compressive creep for example. This is the term used to describe the gradual loss of thickness when foam is placed under load for an extended period of time, this can lead to movement of equipment inside the case. There are ways we can combat this issue, such as properly calculating the load limits of the material used. For instance, etha foam (used for the majority of our case interiors) has a static loading limit of 2.5 psi. Also, spreading the load over a larger area is another way to minimize the effect of compressive creep.
If an interior is not designed properly another issue that comes into play is buckling. This generally occurs when foam has been cut too thin, too tall, or a combination of both. This leads to the energy of an impact to the case not being transferred properly resulting in damage to your equipment. Finally, temperature is a consideration when it comes to cushion design. Etha foam typically retains its performance characteristics over a wide range of temperatures, but extreme cold or heat can cause the foam to become stiffer or softer.
At ECM we take all these factors into account when it comes to interior design. This enables us to provide an interior that performs as well as the case exterior, resulting in the utmost in protection for your equipment.